Wat Is die Sleuteltipes van Elektriese toerusting vir die Industrie?
Industriële fasiliteite is afhanklik van 'n verskeidenheid elektriese toerusting om masjinerie aan te dryf, energie te versprei en veilige, doeltreffende operasies te verseker. Vanaf hoogspanning-transformators tot presisie-motore speel elke stuk elektriese toerusting 'n kritieke rol in die handhaving van produksielyne, die handhaving van veiligheid en die optimering van energieverbruik. Die begrip van die sleuteltipes van elektriese toerusting vir die industrie is noodsaaklik vir fasiliteitsbestuurders, ingenieurs en operateurs wat verantwoordelik is vir die selektering, instandhouding of opgradering van stelsels. Kom ons ondersoek die belangrikste kategorieë, hul funksies en hoe dit bydra tot industriële sukses.
Kragdistribusietoerusting: Voorsien Elektrisiteit Veilig
Kragdistribusie-elektriese toerusting vorm die ruggraat van industriële energiestelsels en bestuur die vloei van elektrisiteit vanaf die rooster of generators na masjinerie en toestelle. Sonder hierdie stelsels sou hoë-spanningkrag van nutslyne sensitiewe toerusting beskadig, wat distribusie 'n fundamentele komponent maak.
Transformators
Transformators is vitale elektriese toerusting wat hoë-spanning elektrisiteit (van die rooster, gewoonlik 11 kV–33 kV) omskep na laer spannings (byvoorbeeld 480 V, 208 V) wat geskik is vir industriële masjinerie. Industriële transformators kom in twee hoofsoorte voor:
- Distribusietransformators: Verminder spanning vir algemene gebruik in fasiliteite, naby skakelgear of masjienklusters geïnstalleer.
- Isoleringstransformators: Beskerm sensitiewe toerusting (byvoorbeeld CNC-masjiene) teen spanningspieke deur die las van die hoofvoorsiening te isoleer.
Hoë-doeltreffendheidstransformators (byvoorbeeld amorfe kernmodelle) verminder energieverliese, 'n sleuteloorwegging vir fasiliteite met hoë kragaanvraag.
Skakeltoerusting en Paneelborde
Laaiskakelstroomkrings beheer, beskerm en isoleer elektriese stroombaane, wat veilige verspreiding verseker. Industriële laaiskakelstroomkrings sluit in:
- Stroomonderbrekers: Skakel outomaties die krag af tydens oorlaai of kortsluiting, om toerustingbeskadiging en brande te voorkom.
- Ontkoppelingskakelaars: Skei handmatig gedeeltes van die elektriese stelsel vir instandhouding, belangrik vir werkers se veiligheid.
- Busstange: Geleidende stange wat krag binne die laaiskakelstroomkring versprei, en hoë strome doeltreffend hanteer.
Paneelborde is kleiner, gelokaliseerde weergawes wat krag na spesifieke areas versprei (bv. 'n produksylie) en stroomonderbrekers huisves vir individuele masjiene. Beide laaiskakelstroomkringe en paneelborde moet voldoen aan streng veiligheidsstandaarde (soos UL, IEC) om industriele omgewings te weerstaan.
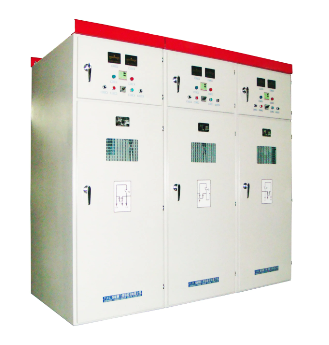
Motore en Aandrywings: Voorsien krag aan industriële masjinerie
Motore is onder die belangrikste elektriese toerusting in die industrie, wat elektriese energie omskep in meganiese beweging om pompe, vervoerbande, kompressors en vervaardigingsgereedskap aan te dryf. Hul werkverrigting beïnvloed direk produktiwiteit en energie-effektiwiteit.
Industriële moteurs
- AC-induksiemotore: Die werkperd van die industrie, gebruik in 90% van toepassings as gevolg van betroubaarheid en koste-effektiwiteit. NEMA Premium® of IE3/IE4-modelle bied hoë effektiwiteit, wat energieverbruik in deurlopende operasies verminder.
- DC-motore: Word gebruik waar presiese spoedbeheer nodig is (byvoorbeeld robotika, rolmeule), alhoewel dit minder algemeen is as AC-motore weens hoër instandhoudingsbehoeftes.
- Servomotore: Verskaf presiese posisionering en spoedbeheer vir outomatisering (byvoorbeeld samestellingslyne, 3D-drukkers), noodsaaklik vir hoëpresisie vervaardiging.
Motore word beoordeel volgens krag (PK) en spanning (gewoonlik 208V–480V vir industriële gebruik), met omhulsels (NEMA 4X, 7) wat ontwerp is om stof, water of gevaarlike omgewings te weerstaan (byvoorbeeld chemiese aanlegte).
Veranderlike frekwensiestuwers (VFDs)
VVFs is elektriese toerusting wat die spoed van 'n motor aanpas deur spanning en frekwensie te varieer, en pas die uitset aan die las aan. Dit verminder energieverspilling—byvoorbeeld sal 'n pomp wat teen 75% spoed werk slegs 42% van die energie gebruik wat dit by volle spoed sou gebruik het. VVFs verleng ook die motorse lewensduur deur die spanningsvermindering tydens aanstart en dit laat sagtweer begin, wat meganiese skok op die toerusting voorkom. Hulle is noodsaaklik vir waaier, pompe en vervoerbande met veranderende vraag.
Beheerstelsels: Outomatisering van Industriële Prosesse
Moderne industriële fasiliteite is verslaaf aan elektriese toerusting vir outomatisering, wat presiese beheer oor masjinerie en prosesse verseker. Hierdie stelsels verbeter akkuraatheid, verminder menslike foute en maak real-time monitering moontlik.
Programmeerbare logika beheerders (PLCs)
PLC's is robuuste rekenaars wat industriële prosesse volgens vooraf geprogrammeerde logika beheer. Hulle ontvang insette van sensors (bv. temperatuur, druk) en pas uitsette aan (bv. motortempo, klepposisionering) om optimale werking te handhaaf. Byvoorbeeld kan 'n PLC in 'n voedselverwerkingsaanleg die vervoerband se spoed aanpas op grond van sensordata om 'n konstante verpakking te verseker. PLC's is krities vir strookverwerking, saamstellingslyne, en enige toepassing wat herhaalbare presisie vereis.
Mens-Machine-Interkantes (MMI's)
HMI's is aanraakskerms of beheerpanele wat aan operateurs toelaat om met PLC's en ander elektriese toerusting te interakteer. Hulle vertoon werklike tyd data (bv. masjienstatus, energieverbruik) en stel handmatige aanpassings in werking, wat hulle noodsaaklik maak vir toesig en foutdiagnose. Gevorderde HMI's integreer met wolksisteme, wat afstandstoezicht op industriële prosesse via slimfone of skootrekenaars toelaat.
Sensore en Aktuateure
Sensore (bv. naderheid, temperatuur, vloei) versamel data oor industriële prosesse, terwyl aktuatore (bv. solenoïedkleppe, servos) fisiese aksies uitvoer volgens beheerstelselbevele. Saam vorm hulle 'n terugvoerslus wat verseker dat prosesse binne gespesifiseerde parameters bly, afval verminder en gehalte verbeter. Byvoorbeeld kan 'n druk-sensor in 'n hidrouliese sisteem 'n aktuator aktiveer om 'n ontlaatklep oop te maak indien die druk bo veilige vlakke styg.
Reserwekragstelsels: Verseker ononderbroke bedryf
Industriële tydverliese kos duisende rand per uur, wat reserwekragtoerusting noodsaaklik maak vir kritieke operasies. Hierdie stelsels voorkom produksieneverliese tydens netuitval of spanningsswankings.
Generators
Industriële generators voorsien reserweekrag, aangedryf deur diesel, aardgas of propaan. Hulle word gekies om die totale fasiliteit se las of kritieke stelsels (bv. verkoeling, noodverligting) te hanteer. Sleutelfunksies sluit in:
- Outomatiese Oorskakelstroomskakelaars (ATS): Skakel krag van die rooster na die generator binne sekondes van 'n uitval.
- Parallelle Vermoë: Verbind veelvuldige generators vir verhoogde kapasiteit, ideaal vir groot fasiliteite of veranderlike vraag.
Dieselgenerators is algemeen weens hul betroubaarheid, terwyl natuurlike gasmodelle laer emissies bied en in lyn val met volhoubare doelwitte.
Ononderbroke Magvoorsiening (UPS)
UPS-stelsels voorsien onmiddellike rugsteun krag deur batterye te gebruik, en vul die leemte totdat generators begin of gedurende kort uitvalle. Hulle beskerm sensitiewe elektriese toerusting (bv. PLC's, bedieners) teen spanningspieke en dataverlies. Industriële UPS-eenhede is versterk om stof en vibrasie te weerstaan, met skaalbare ontwerpe vir groeiende kragbehoeftes.
Sikkerheids- en Beskermingstoerusting: Beskerming van werknemers en bates
Industriële omgewings skep unieke elektriese gevare, wat sorg dat elektriese toerusting met 'n fokus op veiligheid 'n moetwees is. Hierdie stelsels voorkom ongelukke, beskerm masjinerie en verseker nalewing van regulasies.
Boogvlam Beskerming
Boogvlamme—ontploffende energievrystellings as gevolg van elektriese foute—kan ernstige beserings veroorsaak. Boogweerstandige skakeltoerusting, persoonlike beskermende toerusting (PPE) en relais wat foute opspoor en die krag in millisekondes afskakel, verminder hierdie risiko's. Kennetjies wat boogvlamgrense en vereiste PPE aandui, is verpligtend op industriële elektriese toerusting.
Grondfout-afbreekers (GFCI's)
GFCI's skakel die krag af binne millisekondes indien 'n grondfout (stroomlek) opgespoor word, om elektriese skokke te voorkom. Dit is noodsaaklik in nat of geleidende omgewings (bv. voedselverwerking, motorwassers) waar die risiko van kontak met water hoog is.
Opperstroombeskermingstoestelle (SPDs)
SPD's beskerm elektriese toerusting teen spanningspieke wat deur weerlig, nutsnetwerkfluktuasies of masjientoevoer veroorsaak word. Industriële SPD's word by diensingange, skakeltoerusting of naby sensitiewe toerusting (bv. CNC-masjiene) geïnstalleer om oorskot-energie te absorbeer en skade te voorkom.
VRAAG: Elektriese toerusting vir Bedryf
Watter elektriese toerusting is noodsaaklik vir 'n nuwe vervaardigingsfasiliteit?
Kernuitrusting sluit in transformatore, skakelgear, wisselstroom induksiemotors, VFD's, PLC's en back-up generators. Addisionele items (soos servomotors, HMIs) hang af van outomatiseringseise en masjientipes.
Hoe kies ek tussen 480V en 208V elektriese toerusting vir industriële gebruik?
480V-toerusting is meer doeltreffend vir groot motore (50PK+) en verminder geleiergrootte/koste vir hoë lasse. 208V is geskik vir kleiner masjienerie en kommersiële-industriële hibriede (soos pakhuise met kantore).
Watter instandhouding word vereis vir industriële elektriese toerusting?
Motore: Smeerwerk, lagerkontroles, isolasietoetse. Skakelgear: Skoonmaak, draaimomentkontroles, skakelaartoetse. Transformatore: Oliemonstername (vir vloeistofgevulde modelle), koelstelselinspeksies. VFD's: Stofverwydering, termiese skenning.
Hoe kan industriële fasiliteite energiegebruik met elektriese toerusting verminder?
Ruil na hoë-doeltreffende motors (IE3/IE4), installeer VFD's op pompe/waaier, gebruik LED-verligting en integreer energiebestuurstelsels om verbruik te monitoor en te optimeer.
Watter standaarde geld vir industriële elektriese toerusting?
Sleutelstandaarde sluit in NEC (NFPA 70) vir installasie, UL/IEC vir veiligheid, NEMA vir motordoeltreffendheid en ISO vir outomatiseringstelsels (bv. PLC's). Nalewing verseker veiligheid en betroubaarheid.
Table of Contents
- Wat Is die Sleuteltipes van Elektriese toerusting vir die Industrie?
- Kragdistribusietoerusting: Voorsien Elektrisiteit Veilig
- Motore en Aandrywings: Voorsien krag aan industriële masjinerie
- Beheerstelsels: Outomatisering van Industriële Prosesse
- Reserwekragstelsels: Verseker ononderbroke bedryf
- Sikkerheids- en Beskermingstoerusting: Beskerming van werknemers en bates
-
VRAAG: Elektriese toerusting vir Bedryf
- Watter elektriese toerusting is noodsaaklik vir 'n nuwe vervaardigingsfasiliteit?
- Hoe kies ek tussen 480V en 208V elektriese toerusting vir industriële gebruik?
- Watter instandhouding word vereis vir industriële elektriese toerusting?
- Hoe kan industriële fasiliteite energiegebruik met elektriese toerusting verminder?
- Watter standaarde geld vir industriële elektriese toerusting?